When it comes to crafting precise gears, the gear hobbing process stands out as a versatile and efficient method. At HOTEC MOTOR, we take immense pride in our expertise in this intricate process. Gear hobbing machines, which we utilize in-house, play a pivotal role in creating gears with modules ranging from 0.1 to 1.25, ensuring the highest quality for our customers. In this blog, we’ll delve into the fascinating world of gear hobbing and shed light on how this process elevates the precision and efficiency of gear manufacturing.
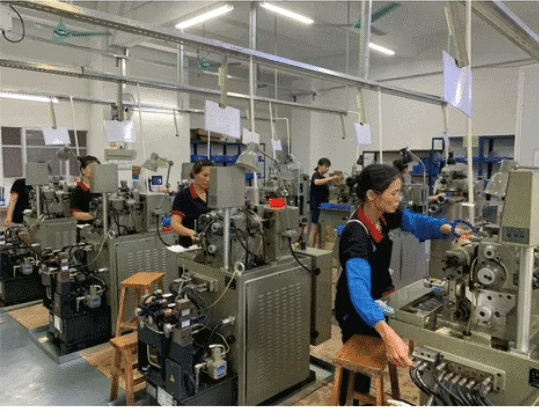
The Foundation: Gear Hobbing Machines
Gear hobbing machines are at the heart of the gear hobbing process. These sophisticated machines are designed to meticulously carve out the intricate tooth profiles that define gears. The process involves the use of a rotating cutting tool known as a hob, which is responsible for shaping the gear’s teeth. Simultaneously, a gear blank is positioned on another spindle within the machine. The relative positioning of these two spindles is crucial and depends on the specific type of gear being manufactured, adhering closely to approved technical drawings.
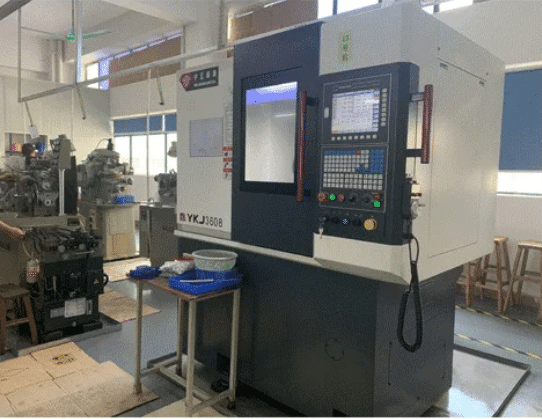
Precision in Action: The Gear Hobbing Process
Once the spindles are correctly aligned and set up, the machine is primed to begin its intricate work. The key is to ensure that the shafts rotate at a speed tailored to the type of gear being produced, optimizing the precision of the process. As the spindles rotate, the hob comes into contact with the gear blank, gradually and precisely cutting the teeth into the gear with the intended depth. It’s a meticulous dance of precision, where each rotation inches closer to the final gear profile.
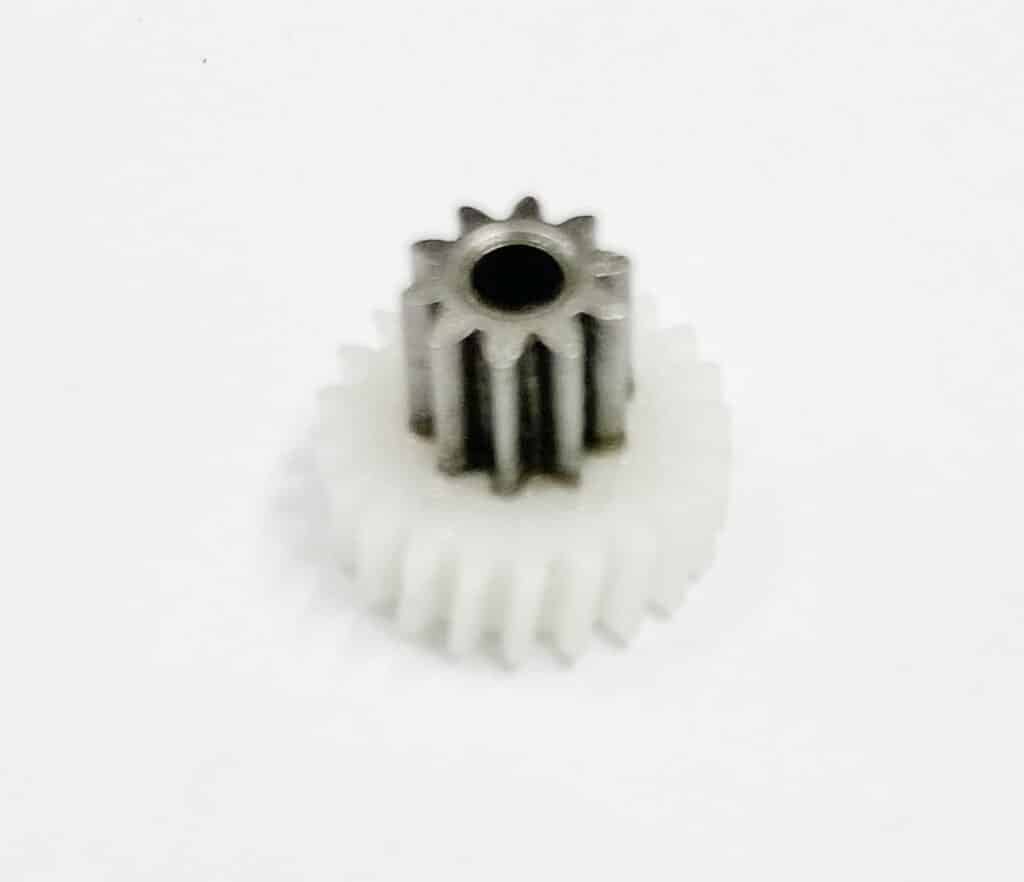
Efficiency Meets Excellence: Gear Hobbing’s Advantages
One of the remarkable advantages of the gear hobbing process is its efficiency. To enhance production effectiveness, multiple gear blanks can be stacked onto the spindle simultaneously. This innovative approach allows the hob to simultaneously cut teeth into multiple gears, saving time and resources without compromising on quality.
Moreover, gear hobbing is incredibly versatile, accommodating a wide range of gear modules from 0.1 to 1.25. This versatility empowers us to cater to a broad spectrum of 10mm-100mm gearboxes, all while maintaining the highest standards of precision.
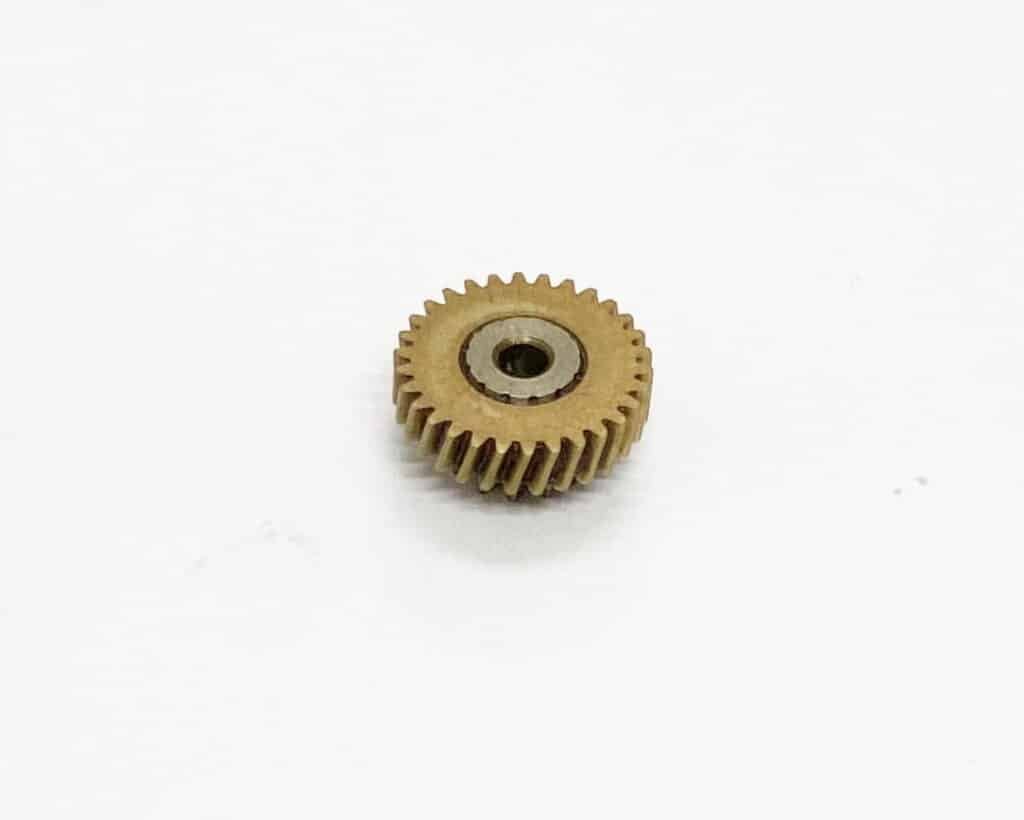
Conclusion: Elevating Gear Manufacturing
The gear hobbing process is not just a mechanical operation; it’s a precision craft. At HOTEC MOTOR, we leverage this process to craft gears that meet and exceed the stringent demands of our customers. With precision as our guiding principle and gear hobbing as one of our core capabilities, we ensure that every gear we produce is a testament to excellence.
In the world of gear manufacturing, where precision is paramount, gear hobbing is our secret ingredient. It’s the process that turns raw materials into finely tuned components, propelling machinery across industries and ensuring that gears mesh seamlessly to drive progress.
For both gears and DC motors are produced in house, we can control our DC gear motor’s quality better, you can totally trust us—where precision, efficiency, and excellence converge.