In the dynamic landscape of micro DC gear motors, a recent collaboration with a U.S. client unveiled a fascinating journey. This customer approached us seeking a motor solution to replace their obsolete Canon precision gearmotor—a 16mm spur gear motor that is no longer available. The catch? It is a critical component in their printer, a product with over two decades of production history.
Navigating the Printer’s Needs
The motors in this printer play a pivotal role, rotating the thread roller of the carbon ribbon in a specific duty cycle of 3 seconds on and 1 second off. The ambitious target: achieving 30,000 duty cycles over the motor’s lifespan.
Choosing the Right Replacement: HT-SOG15A Spur Gearhead Motor
After our engineers evaluated the customer’s given specifications and motor usage information in the printer, we recommended the HT-SOG15A spur gearhead motor. The customer was pleased with our proposal and proceeded to test samples.
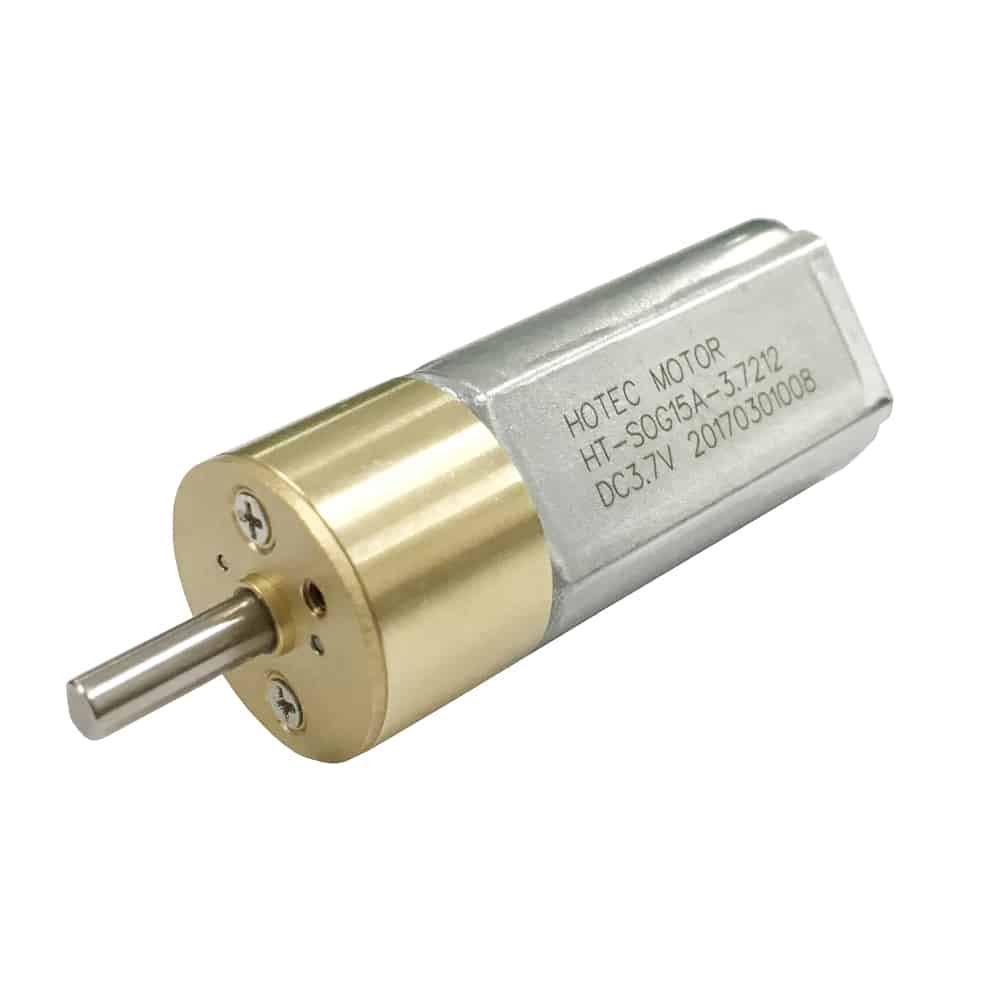
Field Test Challenges: The EMI Conundrum
During the field test, challenges emerged in the customer’s printer circuit. The original design used two op amps to compare the current profile of the motor to determine if the printer ribbon is out or jammed. The customer was experiencing false jams, and upon examining the current profiles, the original engineer had utilized the electrical noise (EMI) level in the current signal as a feature to determine ribbon status. Unfortunately, the original engineer is no longer with the customer’s company, making it impossible to alter the design.
Stage 1: Suppressing Electrical Noise
During the customer’s initial test, print errors occurred due to EMI. The motor, responsible for spinning a spool of thermal tape with about 3,150 inches of tape, encountered false jams in the printer circuit. To address this, we proposed soldering capacitors to the motors to mitigate the noise, providing the customer with two electrical schematic options:
A) Solder one capacitor, and B) Solder three capacitors.
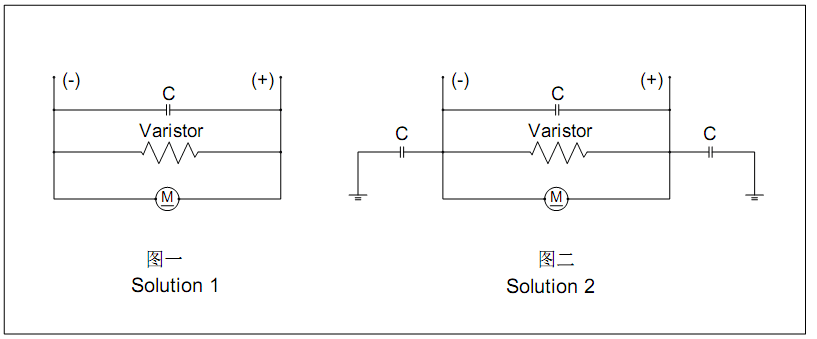
Stage 2: Too Little Noise
Despite the successful mitigation of the Back-EMF spike’s amplitude and frequency, the printer continued to face the same malfunction. The customer indicated that the EMI noise was too little after startup. While normally considered advantageous, the printer’s circuit relied on noise to function, leading to misinterpretations and malfunctions.
Stage 3: Noise Inconsistency Between Startup and Operation
The customer complained about noise inconsistency, with the noise being significant during motor startup and becoming much lower thereafter. This inconsistency was deemed reasonable and unavoidable.
Stage 4: Noise Inconsistency After 30 Minutes
Further testing revealed that after approximately 20-30 minutes of operation, the EMI noise decreased significantly, leading to printer malfunctions. The motor, initially spinning an empty spool, faced challenges as the spool grew larger during operation.
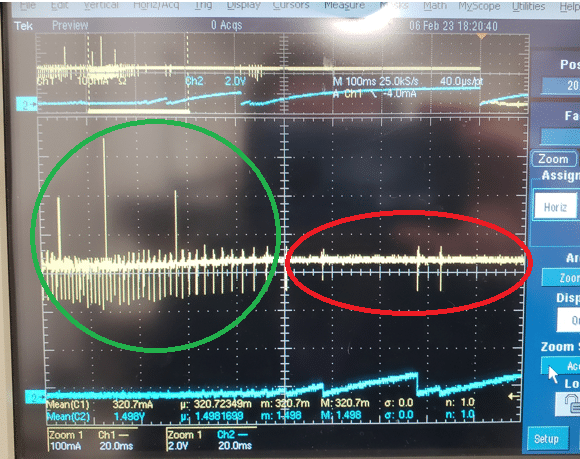
Stage 5: Our Confusion
We found ourselves perplexed. In a typical printer application, as spools increase in size, the loaded torque and current draw from the motors should also increase, resulting in higher EMI noise. However, this was not observed in the customer’s tests, leaving us utterly confused.
Stage 6: Breakthrough
Thanks to the customer’s support, we received valuable information through a test video. It revealed that their test voltage was 7V instead of the rated 12V. Moreover, the 7V voltage dropped to 6V when testing our motors but not when testing Canon motors. Additionally, the loaded current consistently jumped to 359mA before the printer’s power was cut off, irrespective of whether Canon or our motors were used. This led us to speculate that the root cause was a current limit in the customer’s PCB design, information that had not been shared initially. Upon our inquiry, the customer confirmed that the EMI drop corresponded to the voltage drop, confirming our conclusion that the voltage drop, due to their current limit set in the printer, caused low noise profile (Back-EMF) and functional faults.
Stage 7: Introducing HT-SOG15B as the Perfect Replacement
Armed with this newfound understanding, we introduced the HT-SOG15B mini gear motor to the client. Its performance was meticulously aligned to match Canon’s as closely as possible. After a successful field test, HT-SOG15B emerged as the perfect replacement for the Canon motor.
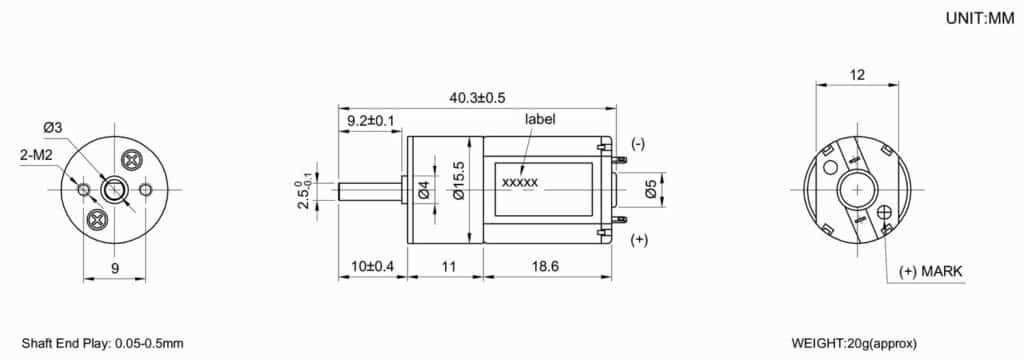
In conclusion, this case study exemplifies our commitment to overcoming unique challenges in micro DC gear motor customization. Through collaboration and persistence, we successfully addressed the intricacies of the printer’s requirements, ensuring a seamless integration of our motor solutions.