Pulse Width Modulation (PWM) is a powerful technique used to control the speed and torque of DC gear motors. By varying the duty cycle of a square wave signal, you can effectively manage the power supplied to the motor, allowing for precise control over its operation. In this blog, we’ll explore how to implement PWM control for DC gear motors and discuss its benefits and applications.
What is PWM?
PWM is a method of reducing the average power delivered by an electrical signal by chopping it up into discrete parts. The average voltage (and hence power) delivered to the load is controlled by varying the duty cycle of the signal.
Benefits of PWM Control
- Precision Control: PWM allows for fine-tuning of motor speed and torque.
- Efficiency: Reduces power loss compared to resistive methods of speed control.
- Versatility: Can be used in various applications, from simple speed adjustments to complex motion control.
Implementing PWM Control
Here’s a step-by-step guide on how to PWM control DC gear motors:
1. Select the Right Components
- PWM Controller: A microcontroller or a dedicated PWM IC.
- DC Gear Motor: Choose a motor suitable for your application. There are many different types and size of DC gearbox motors. It is not easy to find a proper one. You can contact our sales engineers for cost-effective motors that could totally suit your need.
- H-Bridge or Motor Driver: To handle the current and voltage requirements of the motor.
- Power Supply: Ensure it matches the voltage and current needs of the motor and driver.
2. Set Up the Circuit
- Microcontroller: Connect the PWM output pin of your microcontroller to the input of the motor driver.
- Motor Driver: Connect the motor driver to the DC gear motor and power supply. An H-bridge is often used for bidirectional control.
- Power Supply: Ensure your power supply is stable and capable of providing sufficient current for the motor.
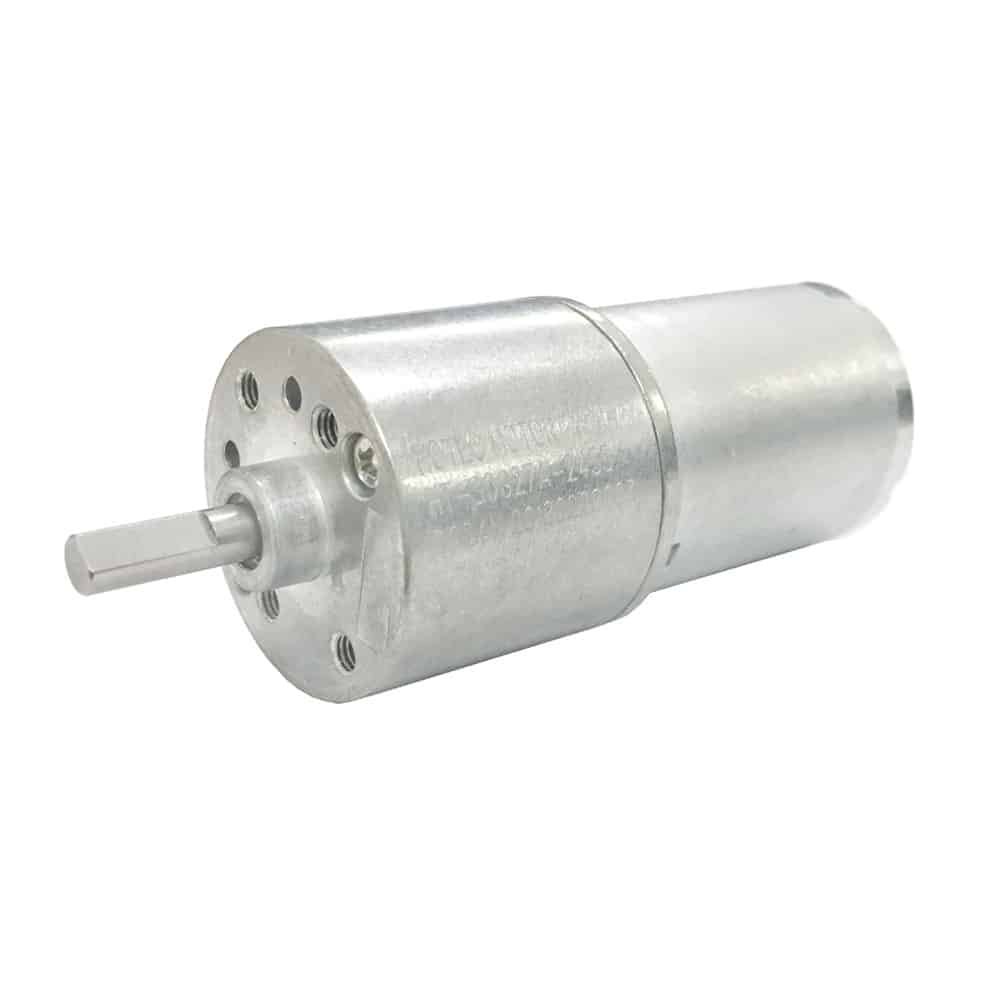
3. Write the PWM Code
Here’s a simple example using an Arduino microcontroller:
const int pwmPin = 9; // PWM pin connected to motor driver
void setup() {
pinMode(pwmPin, OUTPUT);
}
void loop() {
for (int speed = 0; speed <= 255; speed++) { // Increase speed
analogWrite(pwmPin, speed);
delay(20);
}
for (int speed = 255; speed >= 0; speed--) { // Decrease speed
analogWrite(pwmPin, speed);
delay(20);
}
}
This code gradually increases and decreases the speed of the motor using PWM.
4. Adjust Duty Cycle
- Duty Cycle: Vary the duty cycle to control the motor speed. A 0% duty cycle means the motor is off, and a 100% duty cycle means the motor is at full speed.
- Frequency: Choose a frequency high enough to ensure smooth motor operation, typically between 1 kHz and 20 kHz.
5. Test and Calibrate
- Test: Run your setup and observe the motor’s response. Ensure it operates smoothly across the entire range of speeds.
- Calibrate: Adjust the PWM frequency and duty cycle to match the performance requirements of your application.
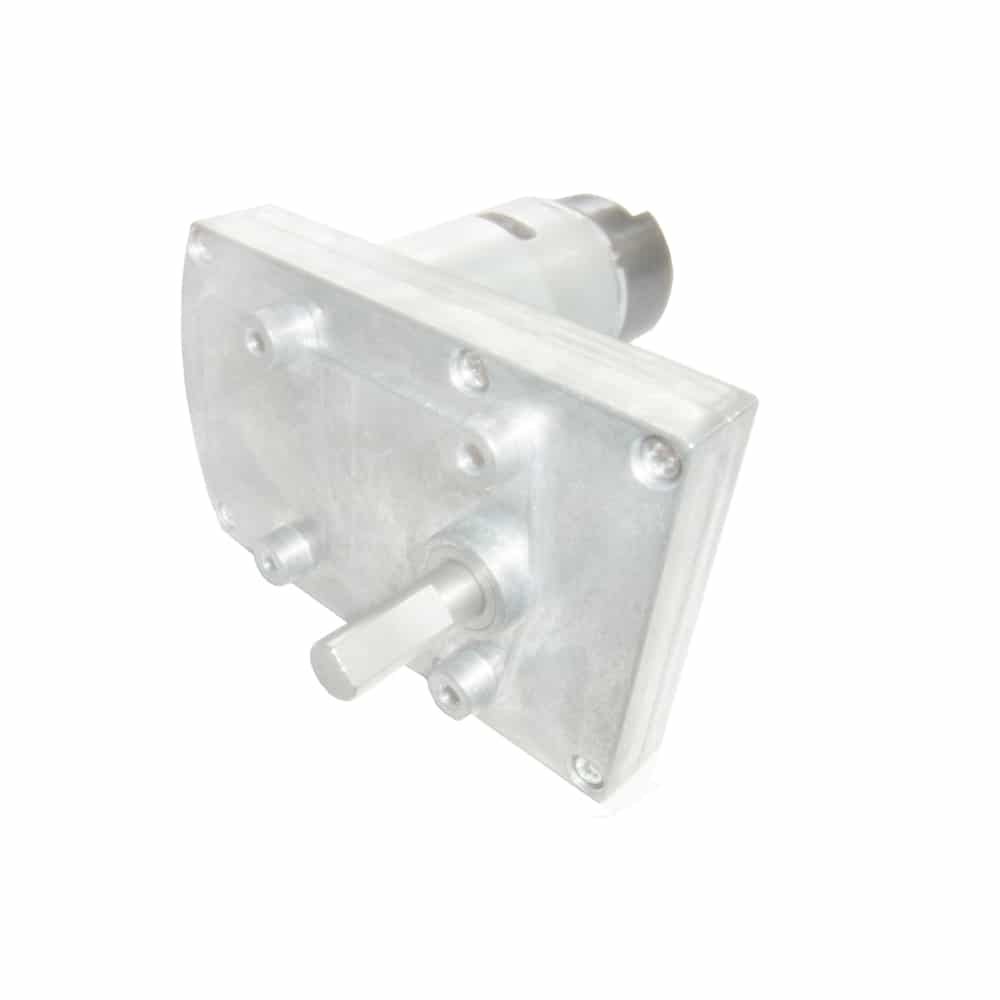
You can also refer to the following video:
Applications of PWM-Controlled DC Gear Motors
- Robotics: Precise control of motor speed and direction.
- Automotive: Adjusting fan speeds, controlling actuators.
- Industrial Automation: Conveyors, robotic arms, and other machinery.
- Consumer Electronics: Fans, toys, and other devices requiring variable speed control.
Conclusion
PWM control of DC gear motors offers precise, efficient, and versatile motor control, making it suitable for a wide range of applications. By understanding the basics of PWM and how to implement it, you can enhance the performance and reliability of your motor-driven systems.
For more information on our range of DC gear motors and how to integrate PWM control into your applications, please contact us. Our team of experts is here to help you find the perfect solution for your needs.